How many people would like a plate punch?
-
- Location: California, USA
- Main keyboard: Ortek MCK-142
- Main mouse: Kensington Expert Mouse
- Favorite switch: Cherry Greens
- DT Pro Member: -
I am talking with a machinist about creating a punch that makes square holes exactly 14x14mm in a plate of 1/8" mild steel.
I think you guys can probably figure out why, but I'll mention anyway that that's the size of the cutout for a cherry MX keyswitch.
If it turns out that a lot of people want them, I could get mine cheaper. I like cheaper.
As one-offs they're quoted at about $75. If I can find 10 or more people who want one, the price would go to around $50.
Do you guys think I could find 10 or more people who'd want one?
I think you guys can probably figure out why, but I'll mention anyway that that's the size of the cutout for a cherry MX keyswitch.
If it turns out that a lot of people want them, I could get mine cheaper. I like cheaper.
As one-offs they're quoted at about $75. If I can find 10 or more people who want one, the price would go to around $50.
Do you guys think I could find 10 or more people who'd want one?
- Wodan
- ISO Advocate
- Location: ISO-DE
- Main keyboard: Intense Rotation!!!
- Main mouse: Logitech G903
- Favorite switch: ALL OF THEM
- DT Pro Member: -
Sounds like a great idea at first but I am worries that punching holes into a steel plate will not give me flat, clean cutouts. How do you use this thing and have you tried it before?
Got some pics from a punched plate?
The potential is great but I need to see it work before I commit myself to this idea.
Got some pics from a punched plate?
The potential is great but I need to see it work before I commit myself to this idea.
-
- Location: California, USA
- Main keyboard: Ortek MCK-142
- Main mouse: Kensington Expert Mouse
- Favorite switch: Cherry Greens
- DT Pro Member: -
I don't have one yet, so no pix of punched plates. Still trying to figure out whether I can order ten. The machinist says this is a routine job and assures me that I can get flat clean holes with it. Evidently this is a variant of something called a 'case punch' which is what they use to make cutouts for mounting plug sockets etc in computer cases. Or at least it's what they used to use before everything went robotic.
- Wodan
- ISO Advocate
- Location: ISO-DE
- Main keyboard: Intense Rotation!!!
- Main mouse: Logitech G903
- Favorite switch: ALL OF THEM
- DT Pro Member: -
It doesn't have to be a MX sized punch but if you can get a hold of a similairly sized punch and make a hole into a steel plate ... I would really be interested in how the hole is actually put in there and how the plate looks after the process.
I remember having to make a hole into a steel sink for the tap and I had to drill a little hole into the center and then mount hole puncher on both sides of the hole and screw both sides together through the drilled hole to cut through the metal. And that sink metal was way less than 1.5mm thick.
Thing looked like this:
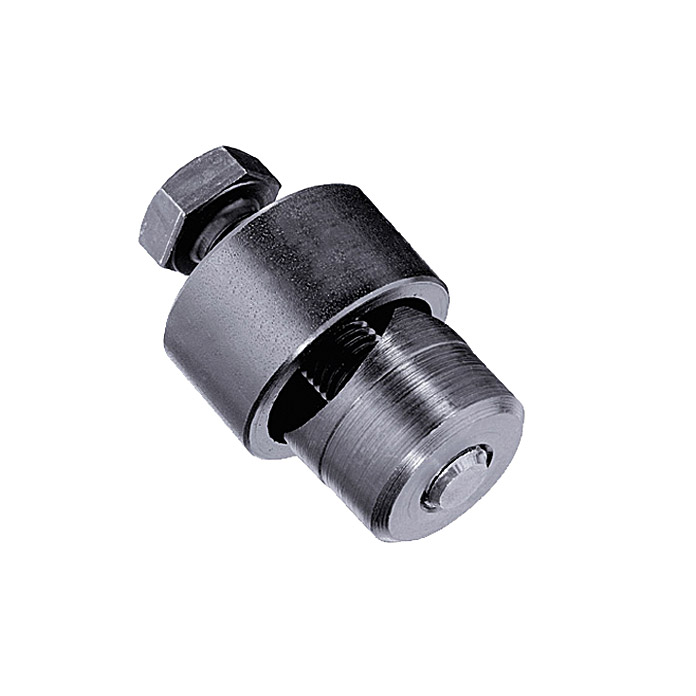
I remember having to make a hole into a steel sink for the tap and I had to drill a little hole into the center and then mount hole puncher on both sides of the hole and screw both sides together through the drilled hole to cut through the metal. And that sink metal was way less than 1.5mm thick.
Thing looked like this:
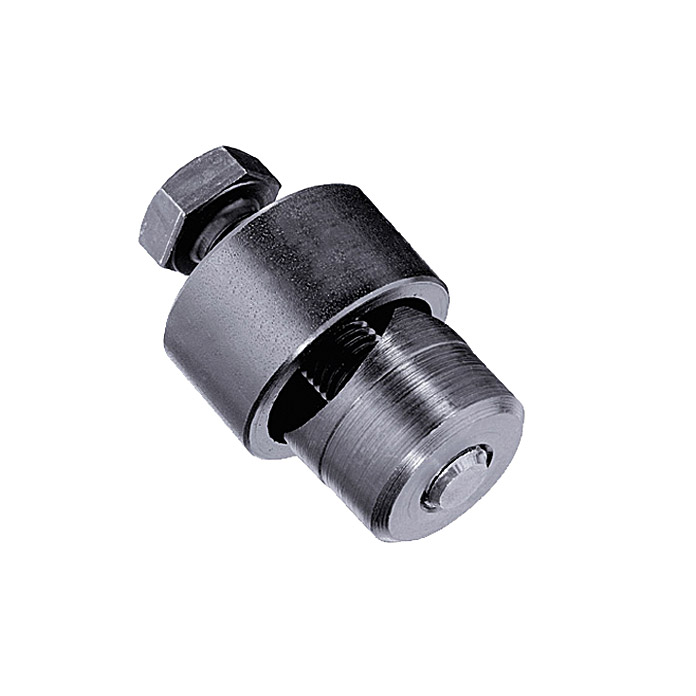
- chzel
- Location: Athens, Greece
- Main keyboard: Phantom
- Main mouse: Mionix Avior 7000
- Favorite switch: Beamspring, BS, Vintage Blacks.
- DT Pro Member: 0086
Wodan get any washer that is about 1,5mm thick and take a look at the edges. One will be a bit rounded and the other sharp. It works like a cookie cutter. Unless I understood something wrong from the OP!
- Wodan
- ISO Advocate
- Location: ISO-DE
- Main keyboard: Intense Rotation!!!
- Main mouse: Logitech G903
- Favorite switch: ALL OF THEM
- DT Pro Member: -
Technically, yeah a cookie cutter ... but we're not talking about cookie dough here. No matter how hard that punch is, we will need significant force to penetrate steel on such a huge surface. So I guess we have to place the plate on an anvil and then hammer on the punch?
Or do we place the place on a soft surface and then hammer through?
Or is it like a giant bolt cutter that we operate with two handles?
Or do we place the place on a soft surface and then hammer through?
Or is it like a giant bolt cutter that we operate with two handles?
- copter
- Last Man Standing
- Location: Helsinki, Finland
- Main keyboard: Filco Majestouch 2 TKL, CM Rapid-I
- Main mouse: SS Rival 100, Corsair M45
- Favorite switch: MX Brown
- DT Pro Member: 0089
I have tool similar that is in the picture. Manual version that works with small hydraulic pump. Our company used it in the past for making holes into cabinets etc during installations if cables / antennas etc were needed to be routed and connected inside a metal casing.
I makes a very clean hole, but in these cases metal has been quite thick and so metal around the hole has been supporting the tool while it's in place.
EDIT: What I'm trying to say is that I'm a bit worried that it might bend the metal around the hole.
I makes a very clean hole, but in these cases metal has been quite thick and so metal around the hole has been supporting the tool while it's in place.
EDIT: What I'm trying to say is that I'm a bit worried that it might bend the metal around the hole.
- copter
- Last Man Standing
- Location: Helsinki, Finland
- Main keyboard: Filco Majestouch 2 TKL, CM Rapid-I
- Main mouse: SS Rival 100, Corsair M45
- Favorite switch: MX Brown
- DT Pro Member: 0089
Tool in the picture at least works in a way that small hole is first drilled, then rod (or bolt like in the picture) is put through it and smaller part is screwed to this rod. On the other side is the larger part (cup). Then these two pieces are pulled together, thus tool making the cut between the larger cup and smaller piece.
- DiodeHead
- Location: Spain
- Favorite switch: Gateron white
- DT Pro Member: -
[youtube]https://www.youtube.com/watch?v=kB8LH_MOZcc[/youtube]
a home usable version of a press punch would be awsome, a manual press wouldn`t make much noise as electrical machinery or a cnc, if your friend could give you some drawings or a picture of a machine that he already have build, would help people to visualize better.
Would it be capable of doing self clinching hardware? thats an interesting feature for metal building of cases.
[youtube]https://www.youtube.com/watch?v=F-xBuQEBYyw[/youtube]
this also has been used in the computer case industry for a long time, before the robot overlord of course.
edit : T_T damm youtube tag, how do they work?
a home usable version of a press punch would be awsome, a manual press wouldn`t make much noise as electrical machinery or a cnc, if your friend could give you some drawings or a picture of a machine that he already have build, would help people to visualize better.
Would it be capable of doing self clinching hardware? thats an interesting feature for metal building of cases.
[youtube]https://www.youtube.com/watch?v=F-xBuQEBYyw[/youtube]
this also has been used in the computer case industry for a long time, before the robot overlord of course.
edit : T_T damm youtube tag, how do they work?
- kbdfr
- The Tiproman
- Location: Berlin, Germany
- Main keyboard: Tipro MID-QM-128A + two Tipro matrix modules
- Main mouse: Contour Rollermouse Pro
- Favorite switch: Cherry black
- DT Pro Member: 0010
Fixed that for youDiodeHead wrote: ↑ a home usable version of a press punch would be awsome, a manual press wouldn`t make much noise as electrical machinery or a cnc, if your friend could give you some drawings or a picture of a machine that he already have build, would help people to visualize better.
Would it be capable of doing self clinching hardware? thats an interesting feature for metal building of cases.
this also has been used in the computer case industry for a long time, before the robot overlord of course.
edit : T_T damm youtube tag, how do they work?

-
- Location: California, USA
- Main keyboard: Ortek MCK-142
- Main mouse: Kensington Expert Mouse
- Favorite switch: Cherry Greens
- DT Pro Member: -
I proposed a hammer punch with a guide/plate support, but he says 1/8 inch metal (he speaks SAE not metric) is too thin for a hammer punch to NOT distort the plate. It would seem fine for the first few holes, but then when you went to mount it you'd find that it's no longer flat.
But it isn't so thin that it requires a pull-through punch that you have to pre-drill a hole for either. What he says is that he'd make a punch that works like a vise-grips. So no need to pre-drill a hole, hardly any noise, and registration (ie, matching up the corners) is taken care of. It would need more "reach" than a regular vise-grip to get to the middle of a plate, but that's apparently not a problem. Knowing that it's only ever going to need to open to 3/16 of an inch and close to -3/16 apparently means you can design a set of vise grips with hellacious leverage.
But it isn't so thin that it requires a pull-through punch that you have to pre-drill a hole for either. What he says is that he'd make a punch that works like a vise-grips. So no need to pre-drill a hole, hardly any noise, and registration (ie, matching up the corners) is taken care of. It would need more "reach" than a regular vise-grip to get to the middle of a plate, but that's apparently not a problem. Knowing that it's only ever going to need to open to 3/16 of an inch and close to -3/16 apparently means you can design a set of vise grips with hellacious leverage.
Last edited by Morituri on 04 Oct 2016, 18:19, edited 1 time in total.
-
- Location: California, USA
- Main keyboard: Ortek MCK-142
- Main mouse: Kensington Expert Mouse
- Favorite switch: Cherry Greens
- DT Pro Member: -
These are mechanically the *kind* of punch he's talking about; these are commercial offerings with a lot of polish and refinement though, not a small-order machine-shop thing. To be clear, this is *NOT* one that he built and the thing we're talking about would lack some of these details. I'm not proposing anything extra like return springs and rubberized grips, so take the pics with a shaker of salt.
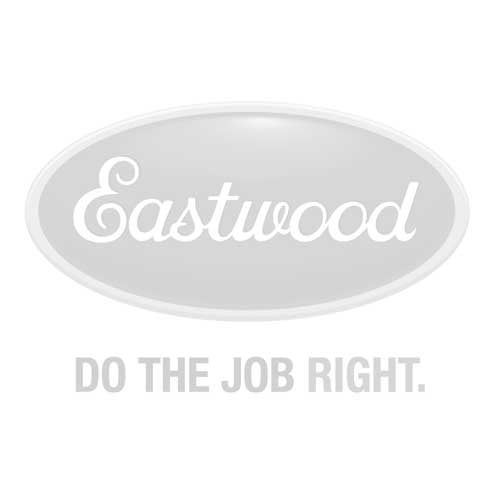

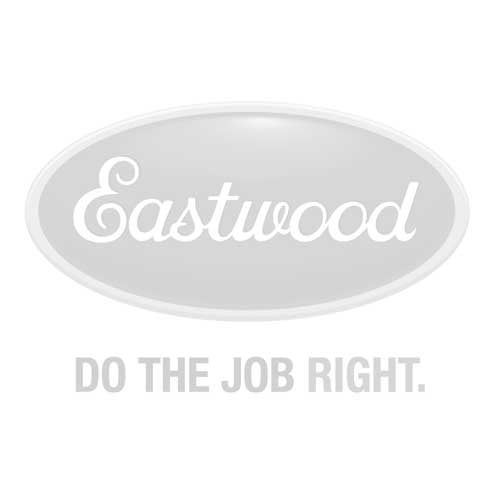

- chzel
- Location: Athens, Greece
- Main keyboard: Phantom
- Main mouse: Mionix Avior 7000
- Favorite switch: Beamspring, BS, Vintage Blacks.
- DT Pro Member: 0086
Seems a bit sketchy to be honest. 1.5mm steel is not easy to perforate, imagine your hand after 20-30 holes...if the tool is stiff enough. If he is willing to back his design (If it's not useable for at least 110 holes you pay nothing) then it might be worth a try. If you plan to use it for more than a couple of boards that is.
- copter
- Last Man Standing
- Location: Helsinki, Finland
- Main keyboard: Filco Majestouch 2 TKL, CM Rapid-I
- Main mouse: SS Rival 100, Corsair M45
- Favorite switch: MX Brown
- DT Pro Member: 0089
Not really worried about my hands, but if doing by hand, then accuracy is probably going to be an issue if making a large array of holes.
-
- Location: California, USA
- Main keyboard: Ortek MCK-142
- Main mouse: Kensington Expert Mouse
- Favorite switch: Cherry Greens
- DT Pro Member: -
The more I communicate with this particular machinist the less I'm confident in him, sorry to say. I'm going to start shopping it around to other shops for bids.
- 0100010
- Location: DFW TX, US
- Main keyboard: IBM 4704 107
- Main mouse: Trackman FX
- Favorite switch: Buckling Spring
- DT Pro Member: -
Morituri wrote: ↑These are mechanically the *kind* of punch he's talking about; these are commercial offerings with a lot of polish and refinement though, not a small-order machine-shop thing. To be clear, this is *NOT* one that he built and the thing we're talking about would lack some of these details. I'm not proposing anything extra like return springs and rubberized grips, so take the pics with a shaker of salt.
With a tool like that, how to you punch holes any further than ~1" away from the edge of the plate?
-
- Location: California, USA
- Main keyboard: Ortek MCK-142
- Main mouse: Kensington Expert Mouse
- Favorite switch: Cherry Greens
- DT Pro Member: -
A tool like that can be made with an 8" throat.
But I think I'm backing off from the guy I've been talking to. Depending on what the next guy says that may not be the type of tool we wind up with at all.
But I think I'm backing off from the guy I've been talking to. Depending on what the next guy says that may not be the type of tool we wind up with at all.
-
- Location: California, USA
- Main keyboard: Ortek MCK-142
- Main mouse: Kensington Expert Mouse
- Favorite switch: Cherry Greens
- DT Pro Member: -
For what it's worth I'm now shopping around a much simpler design; A flat 1 inch by 5/8 inch mild steel bar 10 inches long with an 9.5" deep slot across it. That slot is 1/7 inch wide, to admit a 1/8 inch workpiece. At the tip of the split end, there is a 14mm hole that goes through the split bar. The other bit is a hardened punch, 14mm by 14mm by plenty enough to go through the slot but not by quite enough to go all the way through the bar. Yes, I did submit measurements that allow enough extra (about 7/1000 inch) so that the punch can move in the slot.
The intent of this much simpler design is to operate it with a C clamp (or a bench vise, or whatever). Because the punch doesn't go all the way through the bar, you can squeeze it down absolutely to the thickness of the bar without blunting the punch on the opposite side of whatever you're using to squeeze it. You could also use a hammer I suppose, but you should have a second plate handy in case the hammer blows have some result you don't like.
The intent of this much simpler design is to operate it with a C clamp (or a bench vise, or whatever). Because the punch doesn't go all the way through the bar, you can squeeze it down absolutely to the thickness of the bar without blunting the punch on the opposite side of whatever you're using to squeeze it. You could also use a hammer I suppose, but you should have a second plate handy in case the hammer blows have some result you don't like.
- DiodeHead
- Location: Spain
- Favorite switch: Gateron white
- DT Pro Member: -
Morituri, did you end up building that tool ??
What nobody mention is this:
http://www.atxpowersupplies.com/Sheet-M ... bblers.php
i guess cos they usually max out at 1.2mm thick mild steel, in a 1mm plate scenario for alps could work (not sure, i´ll buy one and tell u guys ).
did anyone use one of these to fabricate a keyboard plate??

What nobody mention is this:
http://www.atxpowersupplies.com/Sheet-M ... bblers.php
i guess cos they usually max out at 1.2mm thick mild steel, in a 1mm plate scenario for alps could work (not sure, i´ll buy one and tell u guys ).
did anyone use one of these to fabricate a keyboard plate??

- lot_lizard
- Location: Minnesota
- Main keyboard: Indy SSK Model MF
- Main mouse: Logitech Anywhere MX
- Favorite switch: Beamspring
- DT Pro Member: -
That one is going to be a bit tough without at least a hobby shop press. The dye you are talking about would work, but you are going to need some significant CONSTANT force to make clean cuts (approx 2.6 tons by my calculations if the dye is flat... ie... a punch) to cleanly make a single 14x14mm punch in 18 gauge mild steel. Any hobby style shop press could certainly handle. You can have an angled dye that acts as more of shear though (square design helps), but I'd be shocked if the best design around gets the force required below a half ton (hand punch is off the table). I think the tool itself could easily hold up for multiple thousand cuts though if going into soft steel or even aluminum if made from proper stock and tempered.
Can I ask what it's desired purpose is? What are you really trying to make with it once it is in your hands? Assuming prototypes, and not small production runs.
Can I ask what it's desired purpose is? What are you really trying to make with it once it is in your hands? Assuming prototypes, and not small production runs.
- CountZero
- Location: Pacific Northwest
- Main keyboard: Infinity Ergodox
- Main mouse: Kensington Orbit
- Favorite switch: The clicker the better
- DT Pro Member: -
I love the idea of a plate punch. A hand squeezed tool doesnt sound workable to me, but an arbor press might be able to provide enought force, supposedly your basic harbor freight special can apply a ton of force. A 14mm square would be fine, but that weird shape with the cut out corners would be even cooler. This would make homebuilt switch plates orders of magnitude more feasible.
(For the uninitiated, this is an arbor press)

Personally I would be willing to pay somewhere in the hundred dollar area for such a tool (press not included). Two hundred would be dicey but not out of the question.
(For the uninitiated, this is an arbor press)

Personally I would be willing to pay somewhere in the hundred dollar area for such a tool (press not included). Two hundred would be dicey but not out of the question.