Hi,
This is more just an open thought than anything. I have seen Model M to Model F conversions for a while. I know that you need a metal top plate to hold barrels etc. This flat metal plate must somehow be curved to interface with a model m back plate.
These top plates require some kind of bending operation to be applied. I know we must know the modulus of elasticity of the metal and the stress strain curve and such.
Anyway I saw this image of Unicomp model m ssk plate. It had this indent in the middle, from possibly bending. I have tried asking unicomp about it but no response yet.
Previous model m/f top plates could be made but required slip rollers or other method to curve. I wonder some simple home shop method can be done. Perhaps some hardware store leadscrew/bolt/nut combo. Something like this.
Then a simple 3d printed fixture in conjunction with hardware store screws could be used to bend this plate. This would allow any metal top plate to be used. Maybe this could be used to make entire modules for model f or m keyboards.
Robb
Curve plate bending apparatus thoughts
- SneakyRobb
- THINK
- Location: Canada
- Main keyboard: KB-5161A, F122, Dc2014, Typeheaven, Beamspring FXT
- Main mouse: MX518 Legendary
- DT Pro Member: 0242
-
- Location: Stockholm, Sweden
- DT Pro Member: 0011
If the bending tool is narrow like that, the plate outside the bent part would be bent sideways near the tool. I believe you would have to either form the entire plate at once, or go back and forth across the plate bending it only a little at a time so as to each time compensate for the error in the previous pass.
- SneakyRobb
- THINK
- Location: Canada
- Main keyboard: KB-5161A, F122, Dc2014, Typeheaven, Beamspring FXT
- Main mouse: MX518 Legendary
- DT Pro Member: 0242
Hi good point, I imagined more like 3-6 of those modules down the lengthFindecanor wrote: ↑19 Jun 2022, 00:25If the bending tool is narrow like that, the plate outside the bent part would be bent sideways near the tool. I believe you would have to either form the entire plate at once, or go back and forth across the plate bending it only a little at a time so as to each time compensate for the error in the previous pass.
- SneakyRobb
- THINK
- Location: Canada
- Main keyboard: KB-5161A, F122, Dc2014, Typeheaven, Beamspring FXT
- Main mouse: MX518 Legendary
- DT Pro Member: 0242
As well there could be some alignment holes drilled into the plate to assist with the bendingSneakyRobb wrote: ↑19 Jun 2022, 00:27Hi good point, I imagined more like 3-6 of those modules down the lengthFindecanor wrote: ↑19 Jun 2022, 00:25If the bending tool is narrow like that, the plate outside the bent part would be bent sideways near the tool. I believe you would have to either form the entire plate at once, or go back and forth across the plate bending it only a little at a time so as to each time compensate for the error in the previous pass.
- jsheradin
- Location: USA
I wonder if the bend radius is similar to any common PVC pipe size. Two nestable tubes (ID of 1 = OD of the other) would work if you cut them into 1/4s or so along the length. You could bend the entire piece at once just by clamping them together. I think alignment dowels would be a good idea so the plate would actually be bent along the correct axis.
Metal of this gauge with this many holes is relatively floppy so it'll conform pretty well as long as it's somewhat close.
Metal of this gauge with this many holes is relatively floppy so it'll conform pretty well as long as it's somewhat close.
-
- Location: Stockholm, Sweden
- DT Pro Member: 0011
Even then you would have to move them around, or the plate would get uneven in-between them.SneakyRobb wrote: ↑19 Jun 2022, 00:27Hi good point, I imagined more like 3-6 of those modules down the length
Another thing to think of is if you're using very low-carbon steel, that the steel should be soft, i.e. annealed before bending. Then you could heat-treat it hard afterwards.
- MathematicalJ
- Location: United States
- Main keyboard: Ergodox Moonlander
- Main mouse: Trackpad
- Favorite switch: MX Browns
- Contact:
You can 100% do this at home. If you have a yoga mat or even carpet, you can get a roller of suitable size. The roller could be PVC or even a rolling pin and doesn't need to be the same size as the curve you want to achieve. Very slowing, bit by bit, roll back and forth on the plate. Small amounts of pressure give small degrees of bend over time, which is what you want. This gives you control over the curve as it forms.
Annealing the metal may not be practical depending on your available tools and type of metal. Steel, for example, requires a sustained temperature >1500ºF. It also needs to cool very slowly, 70ºF/hr, which is far slower than leaving it in open air. Quenching will actually harden the piece.
Aluminum and copper require much more reasonable temperatures, 600ºF-800ºF and 700ºF-1200ºF respectively. (The exact temperature depends on the alloy.) Get the piece glowing orange red, then quench it. Quenching is good for annealing these metals, the opposite of steel.
The bending technique is widely used. I'm not an expert in annealing steel, though, so anyone who is should feel free to chime in.
Annealing the metal may not be practical depending on your available tools and type of metal. Steel, for example, requires a sustained temperature >1500ºF. It also needs to cool very slowly, 70ºF/hr, which is far slower than leaving it in open air. Quenching will actually harden the piece.
Aluminum and copper require much more reasonable temperatures, 600ºF-800ºF and 700ºF-1200ºF respectively. (The exact temperature depends on the alloy.) Get the piece glowing orange red, then quench it. Quenching is good for annealing these metals, the opposite of steel.
The bending technique is widely used. I'm not an expert in annealing steel, though, so anyone who is should feel free to chime in.
- browncow
- Location: Poland
- Main keyboard: Chicony 5161 - blue alps
- Main mouse: microsoft ime3.0
- Favorite switch: Futaba MA
Coming from a sheet metal worker/welder/car body guy what you need for this operation is a sheet metal roller.

or for something simpler, a pipe anvil.
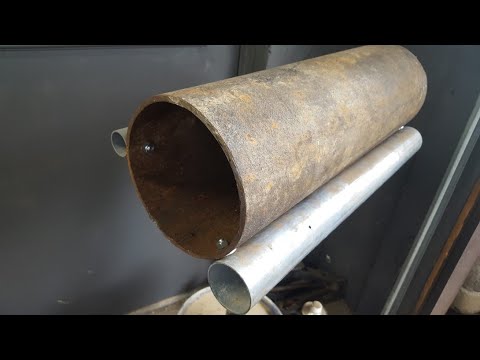
though a roller will be easier to achieve repeatable results with. it doesnt have to be anything fancy, just big enough to fit the piece you need. You can definitely make one yourself

or for something simpler, a pipe anvil.
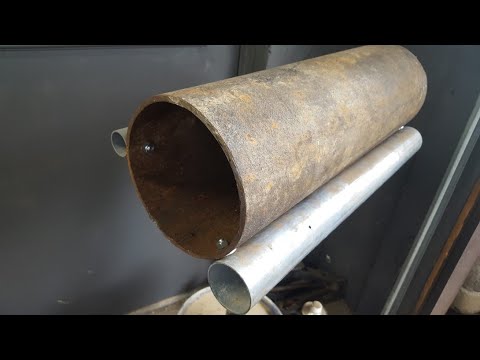
though a roller will be easier to achieve repeatable results with. it doesnt have to be anything fancy, just big enough to fit the piece you need. You can definitely make one yourself
- browncow
- Location: Poland
- Main keyboard: Chicony 5161 - blue alps
- Main mouse: microsoft ime3.0
- Favorite switch: Futaba MA
seems like they even sell very simple rollers on aliexpress https://www.aliexpress.com/item/1005004 ... NhqpeSMvnk
this particular one can roll up to 320mm wide pieces, so too small for a M plate but you could find a better one i guess. but the principle is really simple and making one yourself is basically ordering a few laser cut pieces, and a bit of tubing, about 6 bearings...
this particular one can roll up to 320mm wide pieces, so too small for a M plate but you could find a better one i guess. but the principle is really simple and making one yourself is basically ordering a few laser cut pieces, and a bit of tubing, about 6 bearings...