Heat inserts on Model M Barrel Plate?
- ifohancroft
- Location: Sofia, Bulgaria
- Main keyboard: ErgoDox w/ SA Carbon on Box Jades
- Main mouse: Razer Viper Ultimate
- Favorite switch: Beamspring
- DT Pro Member: -
- Contact:
I have a Model M that needs bolt modding (will go with screws instead of nut/bolt combo) and I saw someone in other post mention the idea of using heat inserts in the barrel plate so it can be in theory safer to open up the keyboard assembly more frequently.
Is that a bad idea? Has anyone tried it?
I remember measuring the thickness of the plate where the screws would go (excluding the bottom row) to be of thickness around 6.5mm and the diameter of spacing between the two "crescent moon" shapes where the screws (or heat inserts) would go to be around 3.5mm so I've ordered heat inserts for M2 screws with an outer diameter of 3.2mm, and length of 5mm, as well as M2 (supposedly) stainless steel screws with 6mm length.
If I try pressing the heat inserts and end up fucking my plate, is there currently where I can get a replacement original one?
Is that a bad idea? Has anyone tried it?
I remember measuring the thickness of the plate where the screws would go (excluding the bottom row) to be of thickness around 6.5mm and the diameter of spacing between the two "crescent moon" shapes where the screws (or heat inserts) would go to be around 3.5mm so I've ordered heat inserts for M2 screws with an outer diameter of 3.2mm, and length of 5mm, as well as M2 (supposedly) stainless steel screws with 6mm length.
If I try pressing the heat inserts and end up fucking my plate, is there currently where I can get a replacement original one?
-
- Location: United Kingdom
- Main keyboard: IBM Model M Square Badge
- Main mouse: Corsair M65
- Favorite switch: Buckling Spring
Give it a go! If you're using 3.2mm outer diameter inserts then the worst that can happen is you'll have to remove them, and then you can almost certainly use 3mm nuts and bolts to complete the mod, as normal.
I personally think it won't work well, but if no ones done it, worth a shot.
I personally think it won't work well, but if no ones done it, worth a shot.
- Muirium
- µ
- Location: Edinburgh, Scotland
- Main keyboard: HHKB Type-S with Bluetooth by Hasu
- Main mouse: Apple Magic Mouse
- Favorite switch: Gotta Try 'Em All
- DT Pro Member: µ
That's the spirit. Do the inserts look something like this?
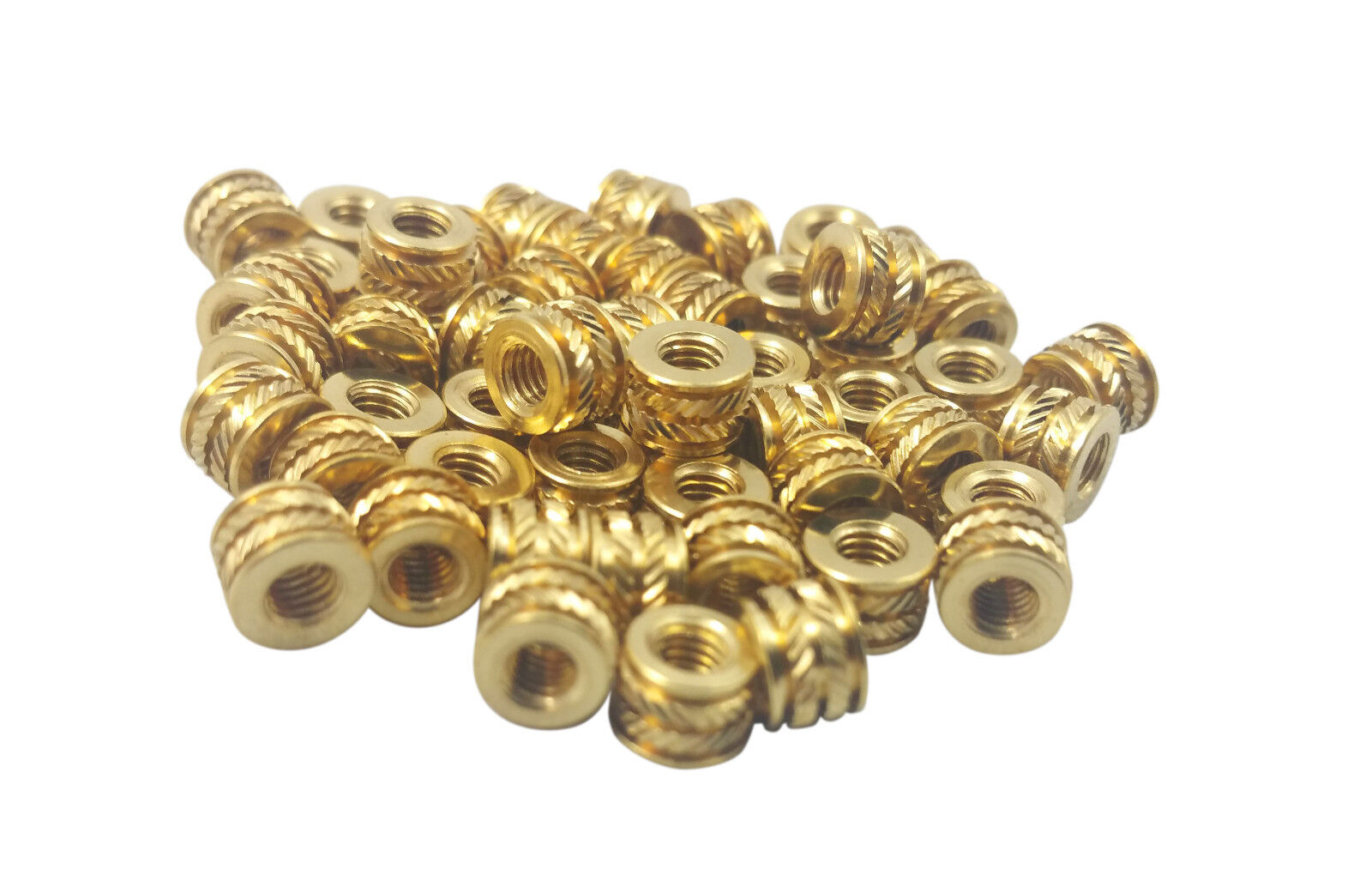
It's a nice idea at least and will be keen to know how well it works. Screwing into brass is surely less worrying than wearing out aged plastic.
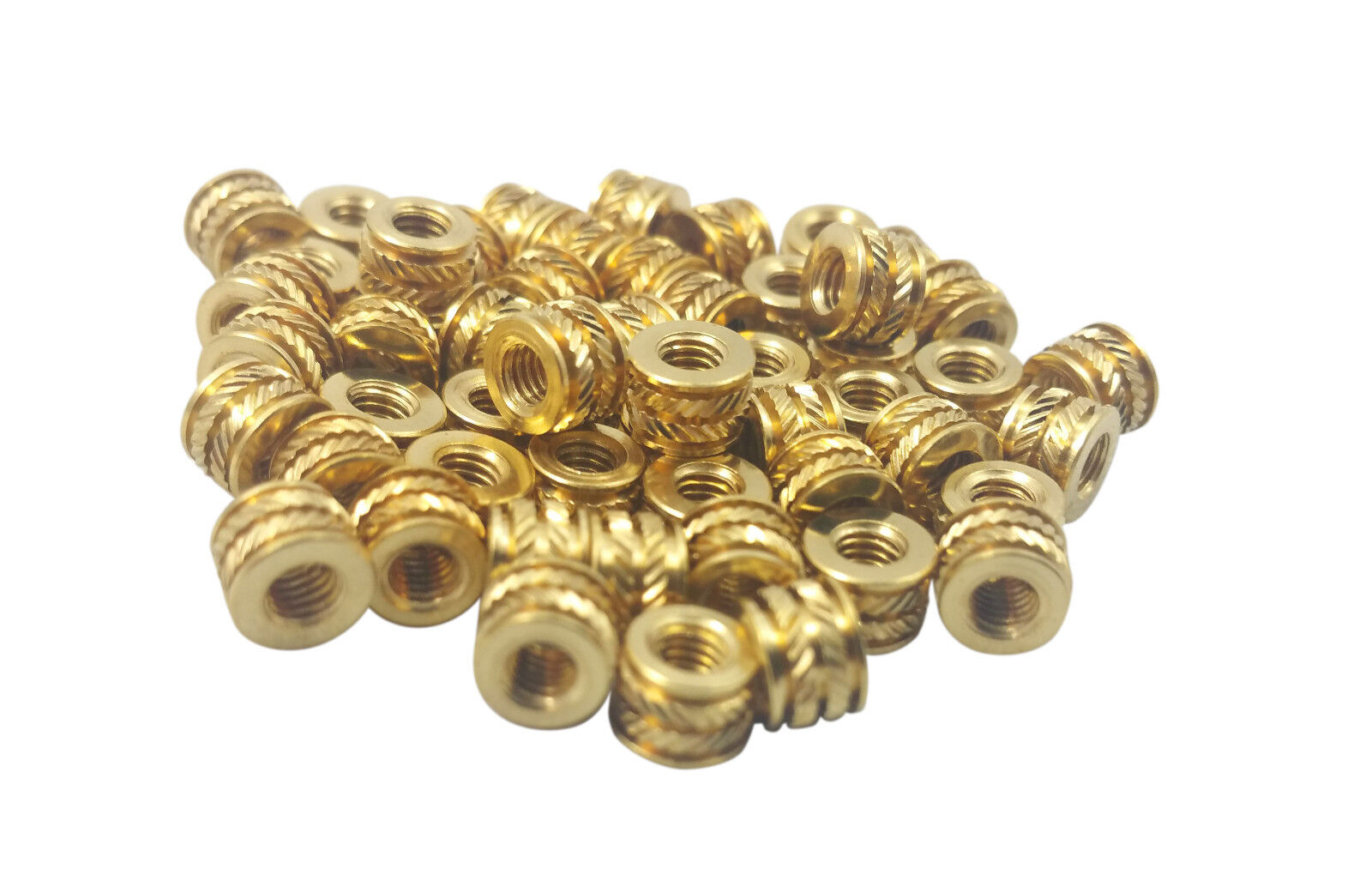
It's a nice idea at least and will be keen to know how well it works. Screwing into brass is surely less worrying than wearing out aged plastic.
- kbdfr
- The Tiproman
- Location: Berlin, Germany
- Main keyboard: Tipro MID-QM-128A + two Tipro matrix modules
- Main mouse: Contour Rollermouse Pro
- Favorite switch: Cherry black
- DT Pro Member: 0010
- clickykeyboards
- Location: United States of America
- Main keyboard: 1395682, IBM model M 1985
- Main mouse: Logitech G500 weighted
- Favorite switch: buckling spring
- DT Pro Member: 0233
- Contact:
I normally use a drill bit of 1.5mm between the plastic crescents when I replace the melted plastic rivets with metal M2 screws. Exactly drilling 3.2mm holes x 56 times into the plastic barrel plate, seems a bit more risky relative to the slight technical advantage gained with "frequent assembly/disassembly".ifohancroft wrote: 27 Nov 2023, 09:58 ,,,diameter of spacing between the two "crescent moon" shapes where the screws (or heat inserts) would go to be around 3.5mm so I've ordered heat inserts for M2 screws with an outer diameter of 3.2mm, and length of 5mm,
One would certainly need to be careful and more precise to not to do more damage than what you are trying to prevent. If you were repeatedly opening the model M barrel plate layers several times a month across several years and if there were alot of excess supporting plastic around the holes, the heat inserts would be warranted.. but I think most would only disassemble a model M keyboard once every year at most?
-
- Location: Germany
- Main keyboard: IBM Model F122
As said above you have to be very careful not to damage the parts that hold the flippers in place. Seems risky.
The heat could also deform the plastic and the flippers would not fit anymore or not move. I would only try on a spare keyboard…
The heat could also deform the plastic and the flippers would not fit anymore or not move. I would only try on a spare keyboard…
- JP!
- Location: United States
- Main keyboard: Currently a Model M
- Main mouse: Steel Series Sensei
- Favorite switch: Beam Spring
- DT Pro Member: 0194
- Contact:
This has been done before! I have yet to try it but would like to try it as I have spare parts and some cracked barrel plates I can use to experiment with.
See:
viewtopic.php?f=7&t=22822
See:
viewtopic.php?f=7&t=22822
- jsheradin
- Location: USA
Unless you're regularly spilling coffee on the keyboard, you probably won't need to disassemble it once screw modded the first time.
That being said, there are a variety of threaded insert designs out there, most aren't melt insert. A self tapping insert would probably work best.
https://www.mcmaster.com/93722A201/

Drill a hole and thread that in with the fancy tool. Gives you a threaded insert with no risk of heat warping.
That being said, there are a variety of threaded insert designs out there, most aren't melt insert. A self tapping insert would probably work best.
https://www.mcmaster.com/93722A201/

Drill a hole and thread that in with the fancy tool. Gives you a threaded insert with no risk of heat warping.
- JP!
- Location: United States
- Main keyboard: Currently a Model M
- Main mouse: Steel Series Sensei
- Favorite switch: Beam Spring
- DT Pro Member: 0194
- Contact:
That's an interesting option. I haven't seen these for plastic before but they do not look like a cost effective option.jsheradin wrote: 27 Nov 2023, 18:16 That being said, there are a variety of threaded insert designs out there, most aren't melt insert. A self tapping insert would probably work best.
I just really like the idea of a keyboard assembly that can be easily taken apart and put back together without concern for a full cleaning, even in the decades to come.
- kbdfr
- The Tiproman
- Location: Berlin, Germany
- Main keyboard: Tipro MID-QM-128A + two Tipro matrix modules
- Main mouse: Contour Rollermouse Pro
- Favorite switch: Cherry black
- DT Pro Member: 0010
I would suggest a Cherry keyboardJP! wrote: 27 Nov 2023, 18:25[…] I just really like the idea of a keyboard assembly that can be easily taken apart and put back together without concern for a full cleaning, even in the decades to come.

- zrrion
- Location: United States
- Main keyboard: F122
- Main mouse: Microsoft IntelliMouse
- Favorite switch: ALPS SKCC Cream
- DT Pro Member: -
- Contact:
why not just get one of those roll up washable boards then if you're that willing to sacrifice key feel for ease of cleaning lol
- browncow
- Location: Poland
- Main keyboard: Chicony 5161 - blue alps
- Main mouse: microsoft ime3.0
- Favorite switch: Futaba MA
I think the best and most reliable solution for this problem would be to make a new steel backplate with threads in the backplate itself. I was thinking about doing that for my own keyboards, as having to use that many nuts is infuriating. (i've done a bit of bolt mods). the threaded inserts Jsheradin proposed look like a good option, IF they would fit, and i'm not sure (as clickykeyboards said the space is very limited, i used M2 bolts instead of self tapping screws, and the drilling wasn't too easy to do even with a proper drill press and having first made some guidance for the drill bit with a soldering iron). The original design just wasn't made with any disassembly/reassembly in mind, and improving on that is not too easy.
- Muirium
- µ
- Location: Edinburgh, Scotland
- Main keyboard: HHKB Type-S with Bluetooth by Hasu
- Main mouse: Apple Magic Mouse
- Favorite switch: Gotta Try 'Em All
- DT Pro Member: µ
Rolling steel into a Model F or M shaped curve is, apparently, quite difficult and very tedious. The only one I've dealt with was the backplate someone rolled me for the XTant, which they swore was the last they'd ever do! It was a bit of a lady-dog to install, as well, as it wasn't really within tolerance and wanted to skew the barrel plate. (I passed it on to DMA, who was more committed and perhaps violent to succeed!) It was untreated and needed something to stop it from rusting, too.browncow wrote: 27 Nov 2023, 23:38 …make a new steel backplate with threads in the backplate itself…
- browncow
- Location: Poland
- Main keyboard: Chicony 5161 - blue alps
- Main mouse: microsoft ime3.0
- Favorite switch: Futaba MA
with a proper metal roller it won't be that hard, but it's a very large radius so you have to just take it slow. If i'd try making one i'd obviously go for zinc plated steel.Muirium wrote: 28 Nov 2023, 11:34Rolling steel into a Model F or M shaped curve is, apparently, quite difficult and very tedious. The only one I've dealt with was the backplate someone rolled me for the XTant, which they swore was the last they'd ever do! It was a bit of a lady-dog to install, as well, as it wasn't really within tolerance and wanted to skew the barrel plate. (I passed it on to DMA, who was more committed and perhaps violent to succeed!) It was untreated and needed something to stop it from rusting, too.browncow wrote: 27 Nov 2023, 23:38 …make a new steel backplate with threads in the backplate itself…
- DMA
- Location: Seattle, US
- Main keyboard: T420
- Main mouse: Trackpoint
- Favorite switch: beamspring
- DT Pro Member: NaN
- Contact:
> (I passed it on to DMA, who was more committed and perhaps violent to succeed!)
Actually I haven't noticed anything like that. Probably USPS has something to do with that - the donor XT arrived in a box that looked like it encountered a steamroller along the way, and the F122's top shell simply cracked from USPS' careful handling.
The box I received the plate in looked intact, but who knows, USPS is a leader in package handling innovation, may be they developed some advanced technologies by then.
Actually I haven't noticed anything like that. Probably USPS has something to do with that - the donor XT arrived in a box that looked like it encountered a steamroller along the way, and the F122's top shell simply cracked from USPS' careful handling.
The box I received the plate in looked intact, but who knows, USPS is a leader in package handling innovation, may be they developed some advanced technologies by then.